Lean management as a tool to improve business efficiency
Business development depends on a number of factors, one of which is the proper management of production processes. It is necessary to set up the entire production chain in such a way as to optimize costs and maximize profits. For this purpose, various concepts are used, one of which is lean management. Its essence lies in the timely identification of weak links in processes and the elimination of losses. Thus it is possible to reduce costs and increase efficiency.
This management model was developed by Toyota Corporation in 1950, but it still works perfectly today. According to lean management, there are seven types of losses in any production process:
1. Overproduction, when a company does not sell the number of products it produces. According to Taiichi Ohno, author of Lean Management, this is one of the key problems that leads to other losses.
2. Excess inventory. In this case, it’s not just finished products in stock, but also unrealized projects and unused materials.
3. Excessive product functionality. This refers to the presence of options that are not used by consumers.
4. Delayed decision-making, waiting for approval. In this case, time is wasted, work is stopped, and the time to deliver the product increases. This often happens during project implementation, when you have to wait for revisions or approvals from management.
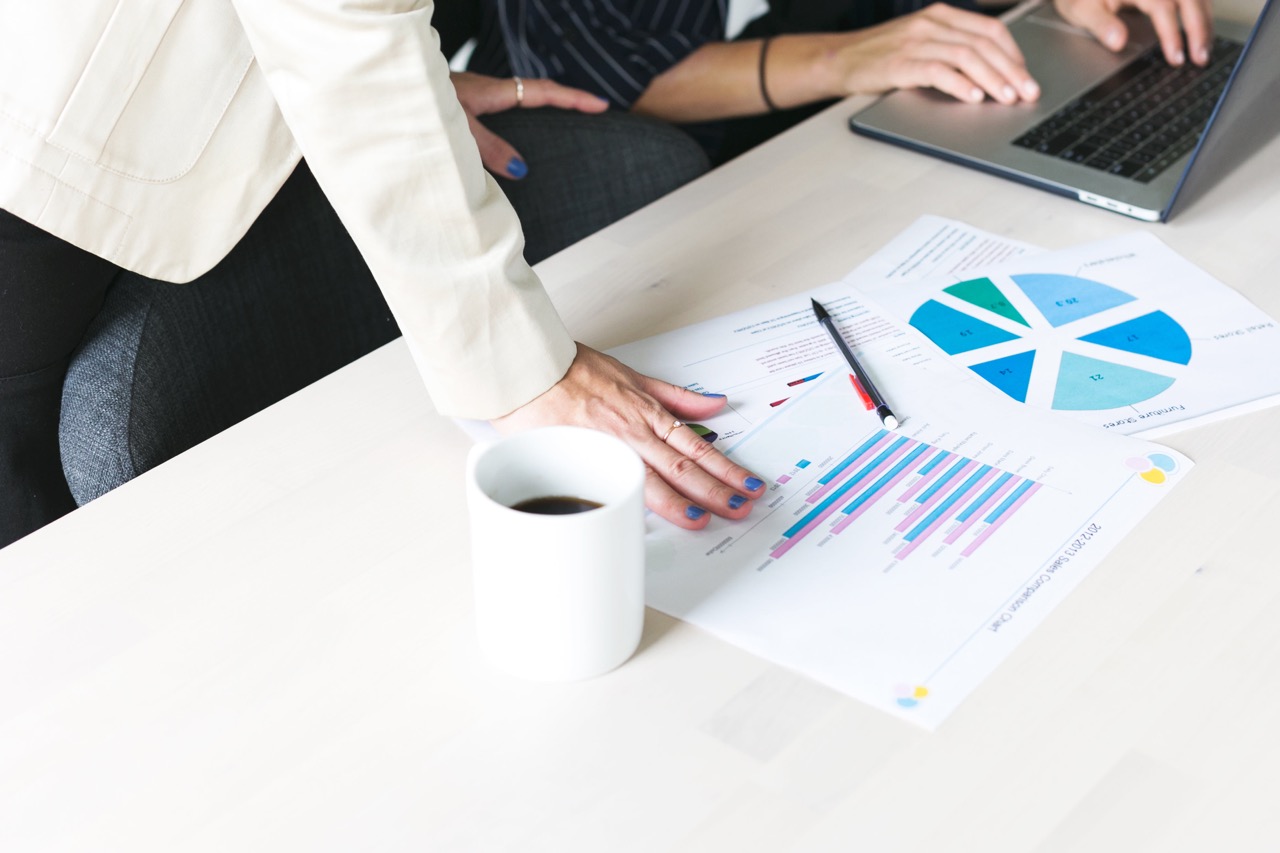
5. Defects or flaws. Additional time and resources must be expended to correct errors. It is possible to reduce the likelihood of errors by implementing a quality control system in the initial stages of work.
6. The presence of unnecessary steps in the work process. This refers to the transfer of responsibilities from one department to another. In addition, losses can occur when a new employee needs to be trained while working on a project. As a result, key processes are idle.
7. Logistics disruptions. These are cases where materials are not delivered on time and there are problems with transportation. In terms of projects, we are talking about irrationally distributed tasks, when you have to work on several things at the same time, which reduces the quality of the result.
Another loss is the unrealized potential of employees, as a result of which they lose interest in their work – and performance drops.
According to the lean management concept, it is necessary to identify all these losses and start processes to eliminate them. And the earlier the problem is detected, the greater the chance of reducing the company’s costs. One of the elements of improvement is the methods of increasing the involvement of employees in the production processes. This is achieved through their regular training, professional development, and incentive systems. By understanding their value to the company and having the right amount of knowledge, an employee strives to improve the quality of their work, which has a positive effect on the development of the business as a whole.